AI and ML Implementation for Manufacturing Plant
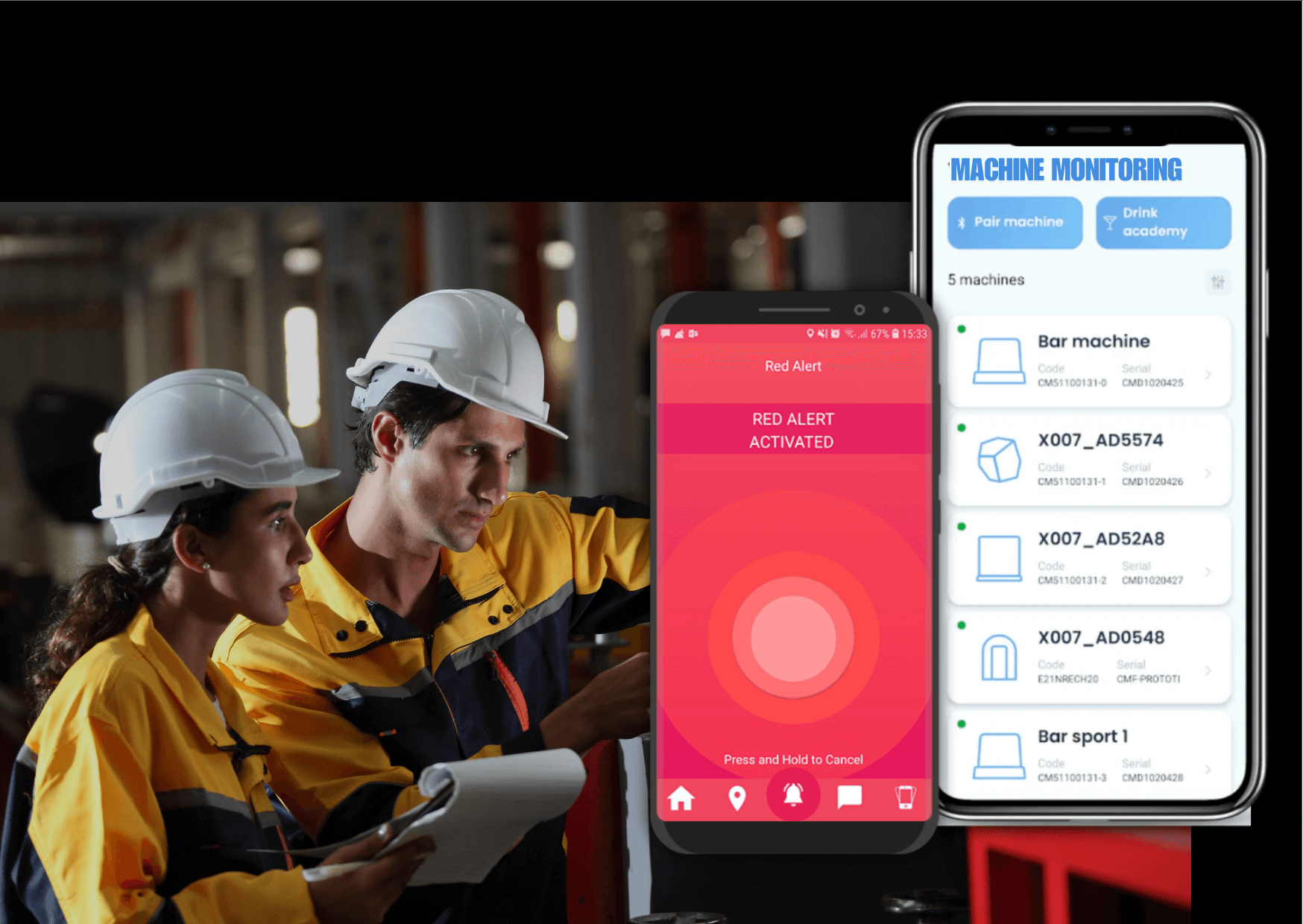
Client Overview
One of the leading Manufacturing plants of cosmetic products in India reached out to us in order to optimize their machinery setting so that the overall maintenance and performance are optimal. They also had few sensors which give optimal and abnormal readings to ensure the flow of energy in machines can be changed accordingly. This while system needs automation, monitoring, and reporting.
Industry
-
Logistics
Platform
-
Web & App
Business Type
-
Enterprise Business
Problem Statement
A gear manufacturer specializing in mechanical equipment faced challenges with unexpected equipment failures, leading to unplanned downtime.
This not only disrupted production schedules but also resulted in increased maintenance costs and reduced overall equipment effectiveness (OEE).
Types of Sensors and Integrations Required:
To address these issues, the following sensors were implemented for continuous equipment monitoring:
- Proximity Sensors: Detect the presence or absence of an object, ensuring proper alignment and positioning of components in manufacturing processes.
- Humidity Sensors: Monitor humidity levels to prevent corrosion and maintain optimal environmental conditions.
- Infrared Sensors: Detect infrared radiation for temperature measurements and presence detection.
- Vibration Sensors: Monitor machinery vibrations to detect irregular patterns indicative of potential mechanical issues.
- Temperature Sensors: Measure equipment and environmental temperatures to identify overheating risks.
Solution Provided by KodMatrix:
1. Data Analysis:
- Outliers were identified and treated using capping techniques to improve data quality.
- Columns causing multicollinearity were removed to ensure model stability.
2. Data Preprocessing:
- Outliers were identified and treated using capping techniques to improve data quality.
- Columns causing multicollinearity were removed to ensure model stability.
3. Model Building & Evaluation:
- Several machine learning models were evaluated, including Random Forest, Gradient Boosting, and SVM.
- Random Forest was finalized due to its superior precision, recall, and overall F1-score.
4. Deployment:
- The predictive maintenance system was deployed on AWS EC2.
- Data storage and management were handled using Amazon S3 for scalability and security.
Results
- Reduced Unplanned Downtime: Proactive maintenance interventions significantly reduced unexpected equipment failures.
- Increased Equipment Lifespan: Early issue detection extended the lifespan of machinery, minimizing the need for frequent replacements.
- Improved Overall Equipment Effectiveness (OEE): Enhanced efficiency contributed to higher productivity and better resource utilization.
Conclusion
The implementation of AI-driven predictive maintenance effectively addressed the gear manufacturer’s operational challenges. This transformation not only resulted in cost savings and improved equipment reliability but also enhanced overall manufacturing efficiency, positioning the company for long-term operational success.